T1 Test to check molten metal flow and trial production

Metal mold temperature approximately 95°C
Temperature during pouring about 1010°C
Molten metal flow is very good.
Molten metal sufficiently fills the mold up to up-hill part for degassing.
Good run of molten metal was observed even when the temperatures varied slightly due to repeated pouring experiment.
The run of the molten metal was about the same with fast and with slow flow of the molten metal supplied to the product part.
A defect was found in trial production caused by shrinkage in the part sandwiched by the core, which is the part that solidifies last.
T2 Teeter mold test
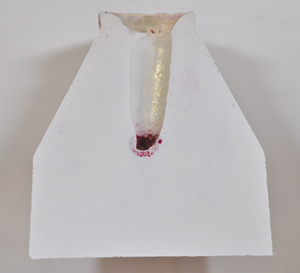
Result: good It can be used for permanent mold casting
Internal shrinkage showed a smooth surface.
In color check at the deepest part of the shrinkage, a small amount of rough texture was observed.It is within the range with no problem.
Thin and deep smooth shrinkage was observed, but we believe the material is suitable for permanent mold casting.
Shrinkage tends to be deeper compared to that of common brass, but this can be accommodated by metal mold plan.
T3 Confirmation of mechanical properties
Tensile strength: 483 N/mm2 Degree of elongation: 45%
Greatly exceeds the standards for common brass and bronze materials.
T4 Analysis and confirmation of molten metal components
Cu | Sn | Pb | Zn | P | Si | Cd | ||
---|---|---|---|---|---|---|---|---|
1. | JIS Standard value | 74.0-78.0 | 0.6Max | 0.25Max | 18.5-22.5 | 0.05-0.2 | 2.7-3.4 | |
2. | Purchased materials | 76.08 | 0.001 | 0.011 | 20.72 | 0.094 | 3.11 | 3ppm |
3. | Before melting | 76.6 | 0.004 | 0.006 | 19.87 | 0.108 | 3.38 | 3ppm |
4. | At the time of test production | 76.3 | 0.004 | 0.005 | 20.19 | 0.11 | 3.33 | 3ppm |
Molten metal management is relatively easy
T5 Confirming processability
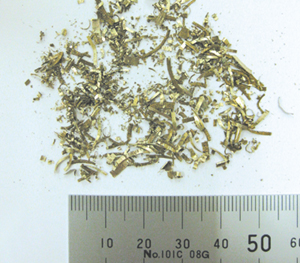
Very hard and tough compared to common brass.
Chips are larger.
Can be processed if the conditions are changed. (Reduce the number of rotations and increase the feed speed.)
T6 Evaluation of pressure resistance of trial production
Result
This trial product was not perfect, but good results were obtained.Effects of metal mold plan are significant.
Preliminary trial production
Leakage was observed in part of the trial production.It was sandwiched by core sand and leaked at what seems to be the final solidification spot. There was no leakage at the part in direct contact with the metal mold.
True trial production
It can be improved through thickness settings and the way molten metal flows based on the metal mold plan.After changing the plan and thickness setting of the product, the results in true trial production were good.
Results and evaluation
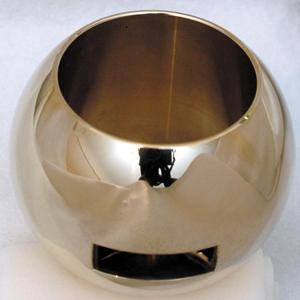
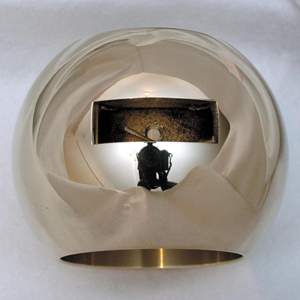
Metal mold castability is good.As it is also developed as a material for permanent mold casting, mass production through low-pressure permanent mold casting can be easily accomplished.
However, the features of the plan must be changed from that for commonly used leaded brass material.
Molten metal flow was good, and mechanical properties were better than common brass in permanent mold casting. Therefore, we can expect a reduced weight metal mold casting by decreased thickness.